生产效能革命:能源管理系统如何重塑制造业竞争力
在全球能源转型和"双碳"目标的大背景下,制造业正面临前所未有的能源管理挑战。据统计,工业领域占我国总能耗的65%以上,其中制造业能耗占比超过50%。随着能源价格波动加剧和环保要求日益严格,传统的粗放式能源管理模式已难以适应发展需求。某汽车集团能源审计数据显示,其生产基地存在高达30%的潜在节能空间,这反映出制造业在能源管理方面的巨大改进潜力。
现代能源管理系统通过对生产设备的精细化管理,实现了能效的全面提升。在某大型装备制造企业的数字化车间,系统接入了超过2000个能源监测点,构建了完整的设备能效画像。通过实时数据采集和分析,企业发现了三大能效提升机会:
设备空载优化:识别出28台存在空载耗能问题的设备,通过智能启停控制,年节约电能消耗150万度。
负载匹配调整:对12台长期处于低效区的加工中心进行工艺参数优化,设备能效提升22%。
预防性维护:基于能耗特征变化预测设备故障,维修响应时间缩短60%,意外停机减少45%。
能源管理系统与生产过程的深度融合,带来了工艺控制的革命性进步。以某化工企业为例,系统实现了:
- 关键参数精准控制:反应釜温度控制精度从±2℃提升到±0.3℃,催化剂使用效率提高18%。
- 能源介质协同优化:建立蒸汽、电力、循环水的智能调配模型,整体能效提升15%。
- 工艺路线创新:通过能源流分析,优化了蒸馏塔操作参数,单套装置年节约蒸汽费用800万元。
能源管理系统构建了多维度的安全防护体系:
- 电气安全监控:某化工厂通过实时监测电缆接头温度,成功预警了5起潜在电气火灾。
- 应急能源保障:关键设备双路供电的智能切换系统,保障了99.99%的供电可靠性。
- 安全阈值管理:设置200多个用能安全参数阈值,实现超限自动保护。
能源大数据正在改变制造企业的决策方式:
- 设备更新决策:某企业依据能效数据,优先改造了能效最低的20%设备,投资回报期缩短40%。
- 产品结构调整:通过产品能耗分析,淘汰了3个高耗能低利润产品,整体利润率提升6%。
- 产能规划优化:新建生产线设计充分考虑了能源管理需求,单位产能能耗降低25%。
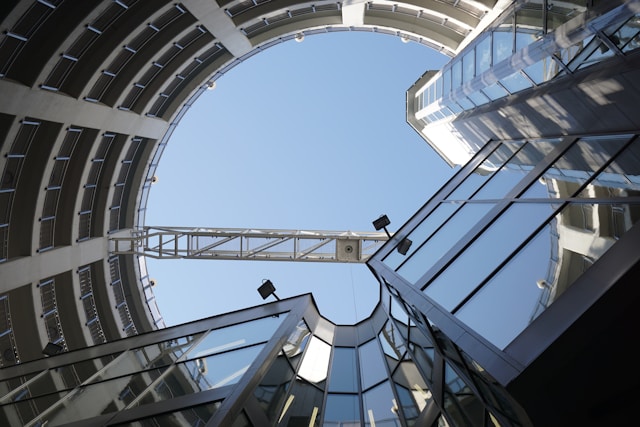
能源管理系统正在引发制造业生产模式的深刻变革。从单一设备到整个生产系统,从操作层到决策层,能源管理能力的提升带来了全方位的效能改进。在智能制造和绿色发展的双重驱动下,那些率先完成能源管理数字化转型的企业,已经建立起显著的竞争优势。未来,随着技术的持续进步,能源管理系统必将成为制造业高质量发展的核心支撑,为企业创造更大的价值空间。