设备全生命周期管理系统的创新实践与价值创造
在工业数字化转型的浪潮中,设备管理正经历着从传统经验驱动向数据智能驱动的深刻变革。现代设备全生命周期管理系统通过融合物联网、数字孪生、人工智能等前沿技术,构建起贯穿设备规划、采购、运行、维护到退役处置的完整管理体系,为工业企业带来全方位的价值提升。
在设备基础管理方面,系统实现了从静态记录到动态管控的转变。通过建立设备数字身份证,完整记录设备技术参数、维护历史、运行状态等关键信息,形成完整的设备数字档案。某大型装备制造企业实施后,设备信息查询效率提升85%,管理响应速度提高90%。智能维护策略引擎基于设备实际运行数据,动态优化维护周期和内容,某汽车制造厂的实践表明,这种精准维护可使设备突发故障率降低70%,平均维修时间缩短50%。
备件与耗材管理模块通过智能化升级实现了库存精益化管理。实时库存监控系统结合设备故障模式和备件使用寿命数据,建立多维度的需求预测模型。某航空维修企业应用后,备件库存周转率提升45%,减少资金占用1.8亿元。全流程追溯体系实现了从供应商评估到报废处置的闭环管理,某石油化工企业借此将备件管理效率提升65%,采购透明度提高80%。智能补货系统基于库存水平和需求预测自动生成采购计划,某半导体制造厂通过此功能将备件缺货率控制在0.5%以下。
设备状态监控是系统的核心价值所在。通过在关键设备部署多参数智能传感器,结合边缘计算技术,实现设备运行状态的实时感知与分析。某重型机械制造企业通过实时监控系统,将故障诊断时间缩短95%。基于深度学习的预测性维护模型能够提前发现设备异常征兆,某风力发电集团的应用案例显示,系统可提前150小时预测设备故障,准确率达到96%,为预防性维护提供了充分时间窗口。
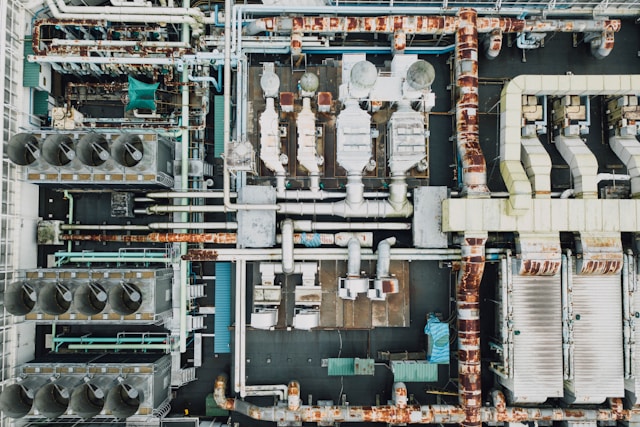
数字孪生技术的应用使设备管理进入虚实融合的新阶段。某核电站构建了与物理设备完全对应的数字孪生体,通过三维可视化技术直观展示设备运行状态,使故障诊断效率提升6倍。移动巡检系统支持工作人员通过智能终端实时获取设备参数和维修指引,某化工园区应用后,巡检效率提升70%,数据采集准确率达到99.9%。
系统为企业创造的价值主要体现在三个维度。在经济效益方面,通过优化维护策略和备件管理,企业运维成本可降低30-45%。某电子制造集团实施系统后,设备综合效率提升22%,年节约成本4000万元。在管理效能方面,数字化工具和标准化流程使管理效率提升60%以上,人为差错率降低90%。在战略价值方面,系统积累的设备运行数据为企业决策提供了科学依据,某工程机械公司通过分析设备数据优化产品设计,使新产品故障率降低48%。
系统实施需要采取科学的推进策略。基础建设阶段重点完成设备联网和数据平台搭建,通常需要6-12个月。某钢铁集团在此阶段部署了10000多个数据采集点,构建了完整的设备监测网络。能力建设阶段着重开发智能分析模型和应用场景,周期约为6-18个月。持续优化阶段通过数据积累和算法迭代不断提升系统性能,这是一个长期持续的过程。
未来发展趋势将呈现三个特征。数字孪生技术的深化应用将实现设备全生命周期的虚拟仿真与优化。5G与边缘计算的结合将支持海量设备数据的实时处理与分析。区块链技术的引入将建立设备管理的可信数据链。这些技术创新将不断拓展设备管理系统的价值空间。
在制造业高质量发展的背景下,设备全生命周期管理系统正从辅助工具升级为战略性的管理平台。通过实现设备管理的数字化、网络化、智能化转型,企业能够在提升运营效率、降低维护成本、保障生产安全等方面获得显著效益。随着技术的持续进步和应用场景的不断拓展,设备全生命周期管理系统必将在工业数字化转型中发挥更加关键的作用,成为智能制造时代不可或缺的基础设施。